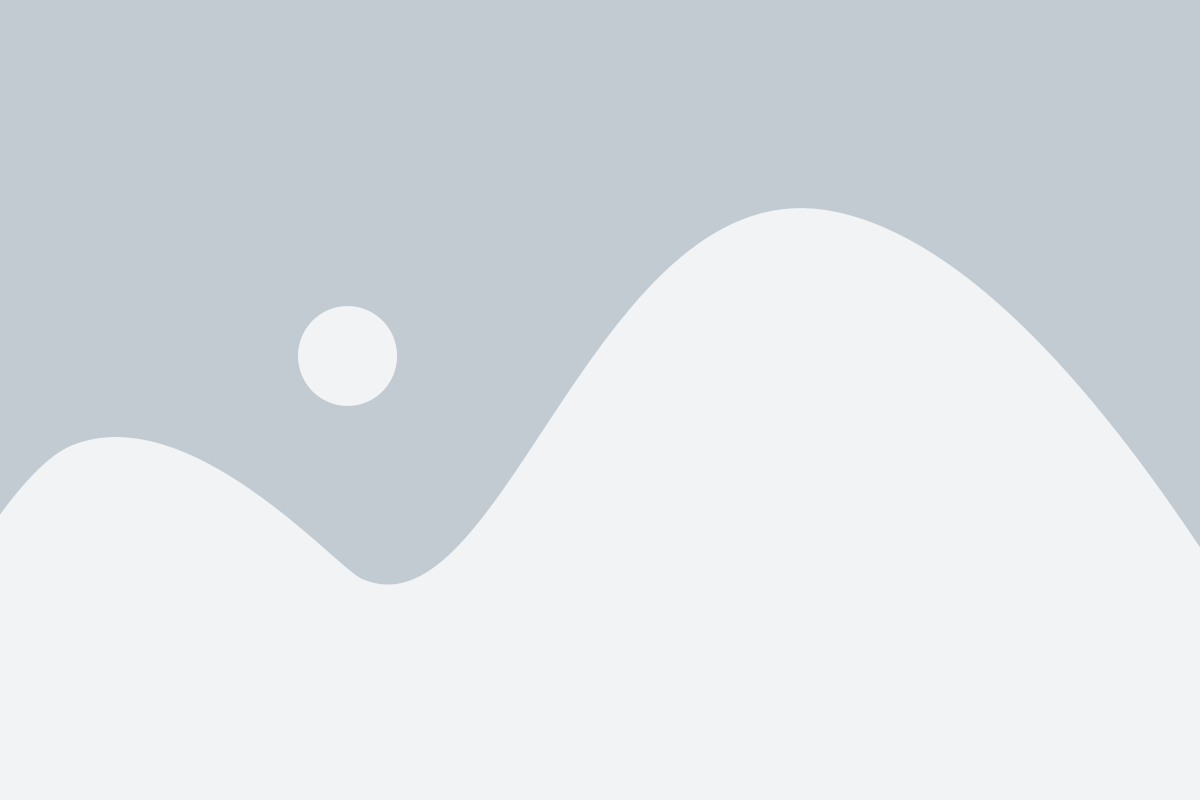
Sanitary Diverter Valve vs. Traditional Valves: What You Need to Know
When it comes to controlling the flow of liquids and gases in various industries, valves are crucial components. However, not all valves are created equal, especially when it comes to applications that require stringent cleanliness and hygiene standards. Sanitary diverter valve This is where sanitary diverter valves come into play, offering distinct advantages over traditional valves, particularly in industries like food and beverage, pharmaceuticals, and biotechnology.
In this blog post, we’ll dive into the key differences between sanitary diverter valves and traditional valves, helping you understand why sanitary diverter valves might be the right choice for your operations.
What is a Sanitary Diverter Valve?
A sanitary diverter valve is specifically designed to meet the high standards of cleanliness required in industries like food processing, pharmaceuticals, and medical device manufacturing. These valves are often used to direct the flow of materials between different parts of a system, such as diverting liquid from one pipeline to another. They are engineered to avoid contamination and facilitate easy cleaning.
Sanitary diverter valves are made from high-quality, corrosion-resistant materials like stainless steel, which makes them ideal for use in environments where hygiene is paramount. They also feature smooth, polished surfaces that prevent the accumulation of bacteria or other contaminants.
What Are Traditional Valves?
Traditional valves, on the other hand, are used in a broader range of industries, including manufacturing, oil and gas, and construction. These valves come in various types, such as ball, gate, globe, and check valves. While they serve similar functions in controlling fluid flow, traditional valves are not necessarily designed with hygiene or ease of cleaning in mind. They are typically made from a variety of metals or alloys depending on the intended use and are suitable for a wide range of environments, not just sanitary ones.
Key Differences: Sanitary Diverter Valves vs. Traditional Valves
- Hygiene Standards
- Sanitary Diverter Valves: Designed to meet strict cleanliness standards, these valves are easy to clean and maintain, reducing the risk of contamination. Their smooth, non-porous surfaces ensure that bacteria and other harmful substances do not accumulate.
- Traditional Valves: While traditional valves are durable and functional, they may not be easy to clean. The surfaces are often rougher, creating opportunities for contaminants to build up over time.
- Material Construction
- Sanitary Diverter Valves: Typically made from high-grade stainless steel, which is resistant to corrosion, pitting, and tarnishing. The materials used in sanitary valves also comply with FDA, 3A, and other industry regulations.
- Traditional Valves: Constructed from a variety of materials such as carbon steel, brass, or plastic. While these materials may be durable in general applications, they might not meet the stringent requirements for food or pharmaceutical industries.
- Design for Cleaning
- Sanitary Diverter Valves: These valves are specifically designed for cleanability. They feature features such as crevice-free surfaces, easy-to-remove seals, and smooth finishes that minimize the risk of contamination.
- Traditional Valves: Typically, traditional valves lack the specialized design for easy cleaning. While some may have removable components, they are generally harder to clean and may require disassembly or specialized tools.
- Compliance with Industry Standards
- Sanitary Diverter Valves: Sanitary valves must adhere to specific industry standards, including those set by the FDA, EHEDG (European Hygienic Engineering & Design Group), and 3A for food and beverage applications.
- Traditional Valves: Traditional valves may not be subject to the same hygiene or material requirements, making them unsuitable for industries that require rigorous sanitary standards.
- Applications
- Sanitary Diverter Valves: Used primarily in industries where hygiene is critical, such as food and beverage, pharmaceuticals, biotechnology, dairy, and cosmetics. They are ideal for applications involving sensitive liquids or gases.
- Traditional Valves: Used in a wider variety of applications, from oil and gas pipelines to HVAC systems and general manufacturing processes.
When to Use Sanitary Diverter Valves
Sanitary diverter valves are best suited for applications that demand the highest levels of cleanliness, such as:
- Food and Beverage Processing: Where contamination could lead to unsafe products.
- Pharmaceutical Manufacturing: To maintain the integrity of drugs and medications.
- Biotech and Medical Applications: To ensure sterile environments for life-saving treatments.
- Dairy Processing: Where cleanliness is a primary concern due to the nature of the product.
When Traditional Valves are Sufficient
While sanitary diverter valves are perfect for the industries mentioned above, traditional valves still have their place. They can be used in applications where cleanliness is not as critical, such as:
- Oil and Gas: Where the focus is on durability and pressure handling rather than sanitation.
- Chemical Processing: Where corrosion resistance is needed, but hygiene may not be a concern.
- HVAC Systems: Where air or water is being moved, but no food-grade or medical standards apply.
Conclusion
In summary, the choice between a sanitary diverter valve and a traditional valve boils down to the specific requirements of your industry. If you’re in an industry that demands high levels of cleanliness and contamination prevention, such as food processing, pharmaceuticals, or biotechnology, a sanitary diverter valve is the clear choice. Traditional valves may work well for general applications, but they won’t meet the hygiene standards necessary for sensitive environments.